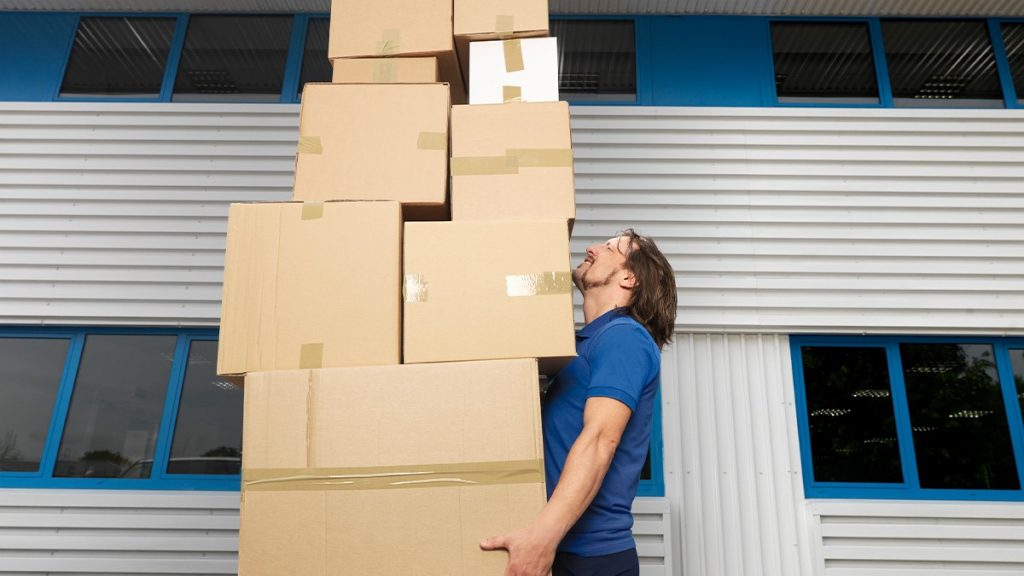
Harvard Business Review has a great article on how Maersk designed their supply chain to be more resilient.
They accomplished this by taking a systems approach to innovation — one that is aligned to the enterprise strategy, solves relevant problems for internal and external customers, develops clear interfaces with partners, and builds and maintains broad organizational capacities. This can bring clarity, resilience, and scalability to efforts to build the supply chain of the future, one that other firms can learn from.
Instead of taking a limited approach to innovation, Maersk’s leaders adopted a systems approach that integrates strategy, processes, and talent in a coordinated way. The only way to ensure agility and resilience is by addressing systemic issues intentionally, focused on the long term, brings together clear priorities, has well-designed repeatable processes, robust governance, and a skilled team.
Specifically, Maersk created a dedicated innovation center in 2021 that has used the following three systems-design principles:
1. Keep a clear focus on enterprise priorities.
The innovation center focused on to port-transload operations — moving the contents of international containers from ocean carriers into 53-foot truck trailers — which was a major bottleneck in North America. It created the Pacific Transload Express, a 117,000-square-foot, 103-door transload facility located a short train trip away from the chaos of Vancouver’s three major container terminals, reducing the volatility of door-to-door times for container shipments from 35 to 75 days to 35 to 40 days. By eliminating more than 100,000 local truck trips per year, it reduced CO2 emissions by more than 15%, advancing Maersk’s goal of being carbon neutral by 2040.
2. Create an effective governance system and clear interfaces with internal and external partners.
The lines of reporting for its innovation center extend up to the C-suite, ensuring that it has the full support of senior management and key operational leaders. There is an innovation council, whose members include Maersk’s North American regional managing director and the unit’s executive vice presidents of operations and corporate operations. External stakeholders providing input to the council include multiple universities (e.g., the MIT Center for Transportation & Logistics), government entities such as the New Jersey Economic Development Authority, the commercial robotics firm Boston Dynamics, and multiple startups. Having the perspective of all these key parties ensures that the innovation center remains focused on the most relevant problems and that it can pivot quickly when an initiative creates new ones.
The innovation group also maintains its own relationships in the VC and startup world to increase its access to new, disruptive technologies and bring an outside-in perspective to their initiatives.
3. Ensure that the center is fully resourced and employs clear and repeatable processes.
Maersk’s leaders thought carefully about the innovation’s center location and chose a dedicated office space in Jersey City, New Jersey, which is far from Maersk North America’s headquarters in suburban Florham Park, New Jersey. The talent they sought was in the metropolitan New York City area, and the urban location was a short PATH train ride from Manhattan. In addition, the site’s distance from the regional unit’s headquarters in Florham Park would provide the psychological and physical separation necessary to ensure that the innovation center didn’t simply default to Maersk’s long-established methodologies.
To keep its teams tied to Maersk’s strategy and remove the need to reinvent the center’s operating model every time it investigated a new idea, clear, repeatable processes were designed and communicated. Instead of leaping from idea to proof of concept, its innovation process begins with the identification of a problem, the stakeholders most affected by it, and its economic and operational impacts.
The Outcome
By November, 2022, Maersk had piloted more than 23 initiatives, seven of which are being rolled out at scale, and two of which were canceled. The net result is a 46% reduction in the lead time variability of shipments from Asia to North America, as well as significant savings. But at an industry conference that same month, North America Regional Managing Director Narin Phol cautioned against complacency. “Supply chain disruption is a constant,” he said. “Don’t take anything for granted.”