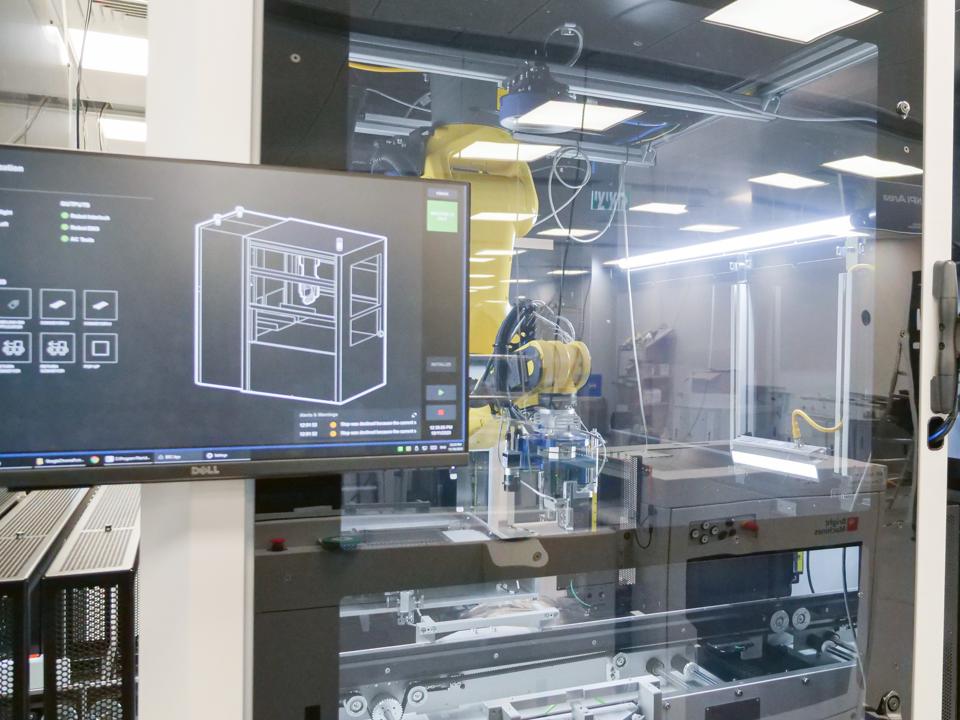
This article in Forbes highlights the inevitability of automation in manufacturing, and why it’s a good thing.
Products are getting smarter. They respond to our touch and voice and adapt to our needs. They are responsive, flexible, and intelligent.
Unfortunately, the same cannot be said about the factories that make them. Our factories are mainly analog; most are still populated by hundreds of people repeating the same task. Neither the processes nor equipment is designed to respond to change, adapt quickly to customer needs, or address quality issues at scale and with ease.
It’s clear that automation is the next giant leap for manufacturing, but its deployment has been stymied for the somewhat ironic reason that automation itself isn’t automated. Instead, machines have to be individually configured and independently managed by human workers. There is no connected flow of information between machines and no method of continuous improvement. This first generation of automation costs too much, takes too long to install, and depends on a small group of experts, making it difficult to scale or replicate.
The logical place to start automating automation is at the back-end of the production line, where assembly, inspection, and testing are still primarily done manually. That requires a combination of technologies to create an integrated system of hardware (such as robotic cells, automatic conveyors, and material feeding systems) and software that leverages computer vision, machine learning, and 3D simulation. The cells provide the arms and legs, and the software provides the eyes and brains. Dexterity and variability are no longer blockers.
See the article HERE. It’s a great read.
#tech #manfucaturing #robotics #automation #business