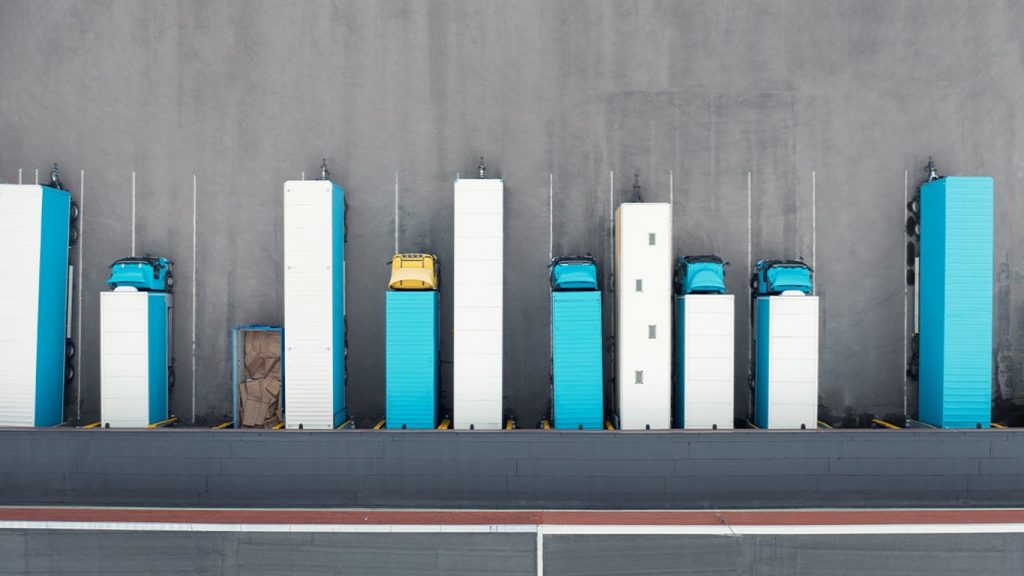
Harvard Business Review has an excellent article on just-in-time supply chains.
Until fairly recently, just-in-time supply chains have worked pretty well, thanks to stable trade conditions and logistics capabilities worldwide.
Turbulence and uncertainty resulting from the Covid-19 pandemic, climate-related disruptions, geopolitical tensions between the United States and China, and the war between Russia and Ukraine have called into question the wisdom of continuing to operate factories on a just-in-time basis that are dependent on global supply chains.
These disruptions are tempting companies to revert to “just-in-case” systems that maintain inventory at various locations in the global supply chain to ensure business continuity.
According to HBR, that would be a mistake.
Just-in-time manufacturing remains the most efficient production system, especially with interest rates rising. Throwing it out and adding inventory willy-nilly would mean hurting performance without necessarily improving resilience.
A better option is to embrace a modified form of just-in-time. It entails creating stockpiles or manufacturing capacity to protect your operation from supply chain disruptions.
Toyota adopted this approach after the 2011 earthquake in Japan’s Fukushima Prefecture. It identified 500 priority parts, including semiconductor chips, whose lead times were very long and, therefore, vulnerable to disruptions. It then built a business-continuity plan requiring its suppliers to stockpile anywhere from two to six months’ worth of semiconductor chips, depending on the lead time. As a result, in the spring of 2021, Toyota did not experience any shutdown or slowdowns while rivals such as Volkswagen, General Motors, Ford, Honda, and Stellantis suffered. Any amount of buffer inventory, however, is still finite, and due to the prolonged chips shortage, Toyota eventually was affected and had to suspend production in some plants a year later.
Companies can revamp their just-in-time supply chains by identifying their contiguous parts that can be run on a just-in-time basis and then connecting these segments via buffers. These buffers could be stockpiles of inventory, excess or flexible capacity, or even warehouses or transportation shared with competitors and other companies. Thus, the company’s supply chain becomes a network of linked JIT segments connected by buffers. Creating such a JIT network requires four steps.
Read the article for more. It’s well worth reading.