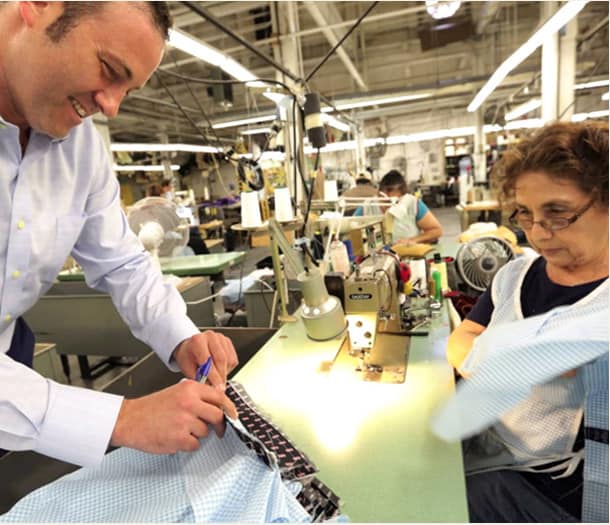
Do you want to see the words “Made in USA” again?
When you make something locally you create value. Local factories energize the economy and invigorate the community by creating jobs, supporting families, and recycling dollars.
Unionwear’s sustainability is built on a foundation of enduring client relationships and workplace satisfaction. We reward our garment workers with union wages and benefits so they have a stake in the long term success of our customers. A living wage can buy the gifted hands of a veteran seamstress. Low employee turnover means knowhow and resourcefulness on the shop floor. High morale means high productivity, lowering costs and speeding up deliveries. Company loyalty translates into pride in workmanship, which can mean pampering every order, every unit that sports our label.
Unionwear has invested heavily in a culture of continuous improvement. We innovate, we tinker, we adapt and we evolve. We’ve expanded into niches suited for the agile, local, “LEAN” manufacturer: small batch manufacturing, lightning fast product development and deliveries, medical packaging, travel gear, safety products, work wear. Now exchange rates and shipping headaches have made local manufacturing attractive again, even for labor intensive hats and bags.
History
Bringing manufacturing back one factory at a time.
Unionwear's expertise has been reviving dead garment factories in NY, NJ and PA by salvaging their machinery and the expertise of their workers, replacing management with lean manufacturing principles and focusing on the markets for their products that prefer domestic manufacturing.
Here is the timeline of other acquisitions and highlights:
-
In 2017, Unionwear successfully accomplished a restructuring financed by Reshoring Capital, which enabled it to raise funds to add new product lines, expand its web offerings, and automate its historically labor intensive operations. By 2018 the company has been able to:
- Acquire the assets of DLX Industries, a Brooklyn, NY manufacturer of binders and portfolios, at auction, and brought on Sales Manager Cindy Kronen and Plant Manger Phil Stern.
- Hire Jose Bellon, who has decades of textile management under his belt at Coach, as VP of Manufacturing.
- Begin manufacturing knit ski hats and scarves at the request of its clients when the last union shop who did so decertified its contract.
- Launch a new web site with nearly 100,000 Made in USA SKUs, that enable its users to order custom products as easily as they would use Amazon.
-
In 2016, Unionwear was the recipient of the Raymond Hopp Lifetime Achievement Award for Excellence in Manufacturing at the annual NJ Manufacturing Awards sponsored by NJ Biz and NJMEP.
-
In 2013, Unionwear acquired its 70,000 square foot facility, and for a time was Newark’s largest privately-held employer of Newark residents.
-
In 2009, The increase in the federal minimum wage and later, the Affordable Care Act, leveled the playing field for union manufacturers and Unionwear was able to compete with manufacturers in right-to-work states for military contracts. Military contracting now represents a third of Unionwear’s business.
-
In 2007, We acquired all the assets of Bag Specialists / ETI Konvex, a manufacturer of backpacks, laundry bags, and high end tote bags for Vineyard Vines, from the Internal Revenue Service. We relocated 90 machines, 40 operators, and Tony Pereira, our bag factory manager with over 40 years experience.
-
In 2000, Unionwear got into the political business when the Al Gore campaign decided to use a union made baseball cap to entice Democrats to donate money through the internet. Since that time Unionwear has manufactured the baseball caps and promotional bags used by every major presidential candidate in both parties.
Over the next several years Unionwear made deals for assets, inventory, and sales with the remaining union hat factories that closed their doors or moved production overseas, such as West Penn, King Louie, and Kraft Hat.
-
In 1998, It became apparent that most of the textile business was going to move their production to Asia indefinitely. After realizing we were one of a handful of (now the only) union label baseball cap manufacturers in the country, we took on the dba “Unionwear” and began marketing our products to labor unions through the promotional products industry.
-
In 1995, we acquired and relocated the entire domestic embroidery operations of the apparel manufacturer Nautica (who relocated the operation overseas) to our (then) Jersey City location, and hired all management and personnel to instantly give us an in house embroidery operation.
-
In 1993, The company started Headcase Hemp Hats, and by 1997 was churning out hundreds of thousands of hemp hats and t-shirts per year.
-
In 1992, Mitch Cahn acquired the assets of London Cap Company, an 80 year old Jersey City baseball cap contractor, in a foreclosure auction and formed New Jersey Headwear Corp. The company started with 6 sewers, and after landing contracts to make caps for Polo Ralph Lauren, Izod, Gant, Barneys, and a number of skateboard and hip hop lines, the company grew to 35 machine operators.
Custom Made
Your concept. Our knowhow. Right here. Right now.
Unionwear can make any type of sewn headwear, bag, binder, or portfolio Send us your product and logo designs and we will help re-engineer them so we can meet your expectations of cost without sacrificing the integrity of your designs. You can also pick one of our dozens of popular (or thousands of unpopular) bag and hat patterns and just choose colors and trims like handles for bags or closures for caps. We do stock the most popular styles of hats blank as well.
After settling on price, guaranteeing a delivery date, and getting a purchase order, we prototype the products and stitch out the logos on new designs when necessary, or just have clients sign off on a long list of specifications on our regular patterns. Fabric and materials are ordered, goods are cut, and are generally embroidered before sewing begins to keep costs low and quality high. A few weeks later, your finished product is subject to rigorous quality inspection and shipped to you or drop shipped to your clients.
Domestic Manufacturing
Tell us what you want and when you want it and give us a budget. We’ll make it happen.
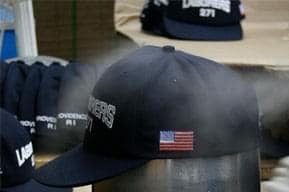
Domestic manufacturers have had to evolve to survive. Unionwear continuously re-engineers our products so we can manufacture locally without sacrificing clients’ profits. During the peak cheap import era there was no attention paid in China to the amount of labor that went into a product. These designs and habits continue even though labor costs are skyrocketing but domestic manufacturers have decades of experience developing techniques that help achieve the integrity of customers’ designs and functionality and still stay within their budgets.
We often expect to undergo several rounds of sampling during product development, which is much easier with domestic manufacturers. For the first time in twenty years, you can actually reduce costs by manufacturing some products or assembling parts of your products domestically. We look for bulky products made from expensive fabrics in quantities large enough to build a dedicated, lean manufacturing production line, but not so large that China is turning them out by the millions.
Lean Manufacturing
Domestic manufacturers can compete by making sure that every minute working is spent creating value. The only way a manufacturer can create value is by making improvements to raw materials that clients are willing to pay for.
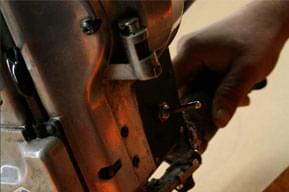
In the garment industry, value is created by cutting and sewing fabric, and decorating finished product. Manufacturers can’t create value by lowering labor costs or building up piecework inventory. Piecework has no value until customers are willing to pay for the finished product. Sewing a shirt is creating value–you are adding value to the fabric. The work done finding, collating, collecting, counting, cleaning, unpacking, carrying, and returning the cones of thread used to sew this shirt is “Non Value Added Work”. It’s an investment with no return and the worker worked just as hard not adding value as he would have if he were sewing. Lean manufacturing means eliminating all non value added work to lower costs, lower prices, and improve delivery times. Unionwear underwent a lean transformation from 2006 through 2008 is featured on the US Department of Commerce’s web site as a lean manufacturing success story.
Social Compliance
When workers earn a living wage and health benefits, turnover is low, morale is high, and they have a stake in the company’s success and identify with its clients.
The “Made in USA” label might not convince consumers to spend more on textiles yet, but labor content in product labeling is as important as ever. Popular buzzwards like Locally Grown, Fairly Traded, SweatFree, Union Made, and Living Wage are all certifications that say something about how and where a product is made. Buying local is important to consumers because it demonstrates that you create value in the community. Taking a stand against sweatshops will reduce exploitation and increase worker rights worldwide. Devastating factory fires continue to occur in unsafe working conditions to this day.
Union Made
The union label is a badge of quality, workplace justice, and living wage.
Unionwear’s employees are represented by Workers United, Local 155, and as such earn health insurance, pension, vacation days, and holidays. It is a myth that “union made” costs more than just “made in USA”. Domestic worker rights laws affecting the federal minimum wage, family leave, and equal pay, and affordable health care passed during Democratic control of Congress narrowed or eliminated cost differential between union and non union domestic factories.
Unionwear’s Clients
The Made in USA Label allows any business to partner with the most valuable brand in the world—and the value of that label exceeds its cost more and more.
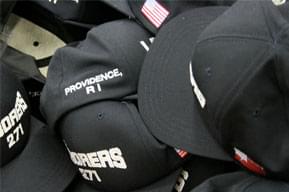
Unionwear sells through a nationwide network of thousands of promotional products distributors.
For years, Unionwear had focused on providing products to clients requiring products to be made in USA, so we were not forced to compete with imports on price. The US military and federal government accounted for a third of our business, with clients like labor unions and presidential campaigns representing much of the balance.
However, the era of cheap imports is over. Inflation, labor unrest, and burgeoning consumer demand in Asia, the weak dollar and fears of the artificially devalued Yuan, and transportation costs and headaches have led textile companies to hedge production by including domestic components. As the premium paid for domestic production shrinks, more and more markets are enforcing labor standards in their procurement: Colleges. Federal, state, and local governments. Corporations with strong union workforce for employee gear. Nonprofits. Since 2011 Unionwear has even seen a surge in contract work for the garment business.